What have been tested ?
In the project, a whole Work Package is dedicated to the safety of the new high pressure type V tubes trailer. This will ensure that the risks are assessed from the design and conception phase of the trailer to keep them to an acceptable level. The following methodology, focused on the use of type V tubes and high pressure, is applied in the project.
Scenario Identification
Assessment
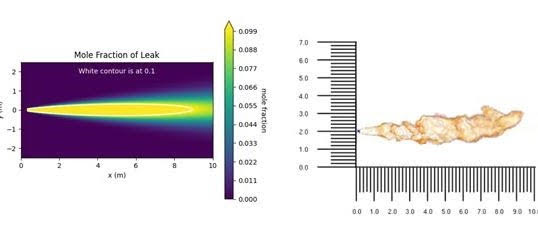
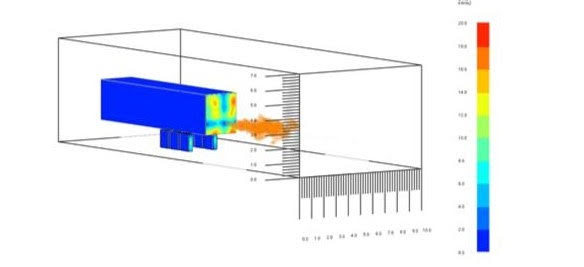
As a first step, it was essential to identify the main failure scenarios likely to be faced on the trailer : it is related for example to thermal aggression (inflammation or exposure to a fire in the vicinity), thermomechanical constraints (shock, deformation) or loss of containment. A list of 5 identified main operational failure scenarios has been established, based on an analysis of the components and the operations, and on an accidentology review. This list was later reduced to a final shortlist of 3 dimensioning events :
- Full bore rupture of the tubes trailer hydrogen filling hose
- Leakage on the tubes trailer hydrogen filling hose
- Leakage on the pipings of the trailer
Based on these scenarios, the severity of their consequences has been carried out : it either consists in estimating the associated distances of effects, as well as evaluating the efficiency of the proposed safety barriers and mitigation means to deal with these hazards. Different approaches have been adopted.
Then, more complex tools of numerical simulation (like CFD) have been employed. These simulations can handle external elements like the trailer itself or its environment (e.g. the other tubes, the congestion nearby the release, the material properties, safety barriers). Currently, the simulated scenarios have only considered the trailer and the position-orientation of the release to evaluate the safety distances to anticipate (see example with figure below). It was shown that the vertical flames caused by leakages on the trailer pipings can trigger greater hazards than horizontal flames located at the gas cabinet : beside the congestion, this can be explained by the higher lengths of the flame and the possibility to radiate on components located beyond protective screens or mitigating obstacles.
Laboratory scale
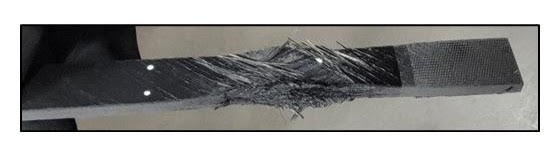
To increase the reliability of the safety simulations and thus the level of safety of the new type V tubes, it is crucial to comprehend the accurate thermomechanical behaviour of the material used in the cylinders. For this purpose, lab scale tests have been started on samples from tubes to dispose of representative data of the structure under different temperatures and after fire exposure (see sample at the end of the test below).
These data will feed different thermomechanical models predicting variations of material stiffness and strength as a function of the temperature and its degradation. Besides, a time-to-burst of a set of tubes representative of a module in a fire will be assessed.
These models can then be applied in the CFD simulations to get more accurate predictions of the trailer level of safety.
Next Step : Large scale : Behaviour of a set of type V tubes exposed to fire
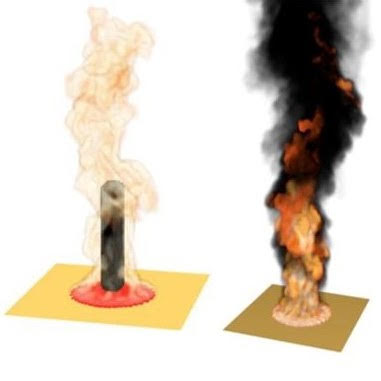
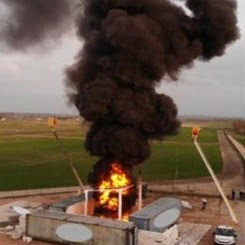
At the end of the project, two full-scale fire tests will be performed to ultimately prove the safety of the new type V tubes once integrated in the trailer.
First, an intermediate bonfire test will be carried out on a tube alone in order to confirm and, if needed, improve the safe behaviour of the tube, i.e. a leak of the hydrogen and no burst releasing hydrogen rather than bursting (see figure of the test plant below). After success, a standardised fire test will be performed on a set of 3 tubes representative of the integration in a trailer to assess the behaviour of a bundle of type V under a typical fire and assess the efficiency of the proposed barriers on a trailer.
These fire tests will also be simulated using the CFD code Fire Dynamics Simulator. The agreement between the numerical and experimental behaviour will make it possible to improve existing tools, to assess whether there is a need to develop new ones, or to validate current tools for such developments.